So What’s the Deal with Tiger’s New Putter; Whoops, I Mean His Old Putter
Ugh, I am so sick of hearing about Tiger’s new Nike putter, which seems to now be his old putter, and I am a guy that likes hearing the announcers talk about the equipment being used (and I actually do like the putter). Despite my disgust, I bet the Nike Golf website’s traffic blew-up this weekend and I am sure sales spiked. So what do I do…. talk more about it of course by looking into the intellectual property aspects of this putter design.
Well, there is no doubt that Nike values the intellectual property concerning the design because they have invested some change in protecting the design. So far they have no less than 2 issued utility patents directed to aspects of the face (USPN 7717801 & 7713139), at least one design patent on the face design (USPN D605242), and at least six pending utility patent applications, which is not unheard of for a popular putter.
The utility patent closest to the actual product is USPN 7717801 titled “putter heads and putters including polymeric material as part of the ball striking face,” which describes the invention as:
The design patent is USPN D605242 and is directed to the unique face layout seen below.
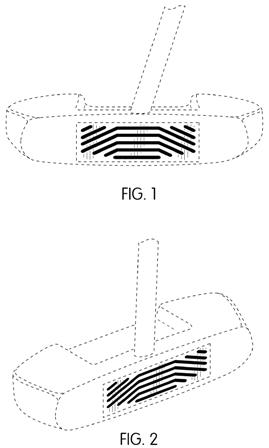
Lastly, one of the published applications (US Pub. No. 20100087269) discloses an interesting face plate design alternative and contains the following drawings and description:
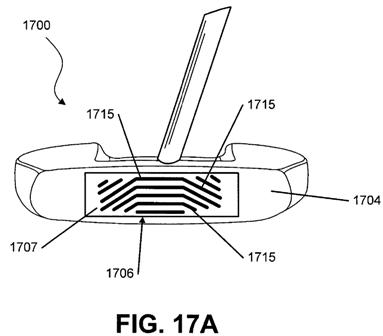
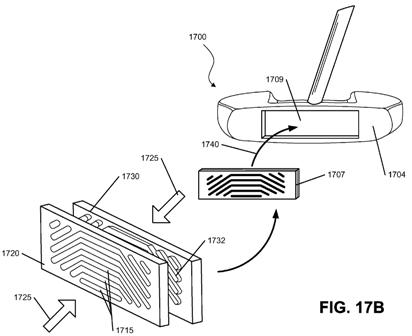
Dave Dawsey - Watching Golf Putting Patents
PS – check out additional putter patents HERE
Well, there is no doubt that Nike values the intellectual property concerning the design because they have invested some change in protecting the design. So far they have no less than 2 issued utility patents directed to aspects of the face (USPN 7717801 & 7713139), at least one design patent on the face design (USPN D605242), and at least six pending utility patent applications, which is not unheard of for a popular putter.
The utility patent closest to the actual product is USPN 7717801 titled “putter heads and putters including polymeric material as part of the ball striking face,” which describes the invention as:
Putters include a putter body having a ball striking face member made of a material having a first hardness characteristic. A cavity is defined in the putter body behind the ball striking face member, and plural openings are defined in the ball striking face member extending rearward with respect to the ball striking face member and into the cavity. A polymeric material at least partially fills the openings and the cavity, wherein the polymeric material has a second hardness characteristic that is softer than the first hardness characteristic. The ball striking face member and the polymeric material exposed in at least some of the openings provide a ball striking surface of the putter. The ball striking surface may include grooves or scorelines to affect the launch angle, spin, and/or roll of the ball during a putt. Methods for making such putter devices also are described.
The design patent is USPN D605242 and is directed to the unique face layout seen below.
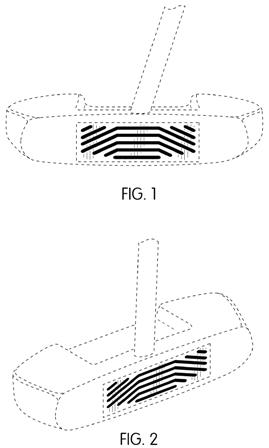
Lastly, one of the published applications (US Pub. No. 20100087269) discloses an interesting face plate design alternative and contains the following drawings and description:
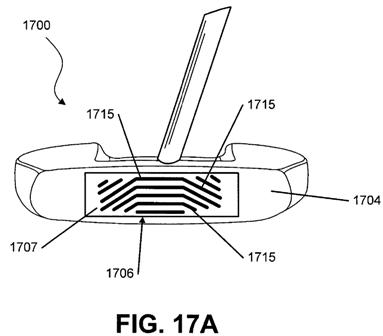
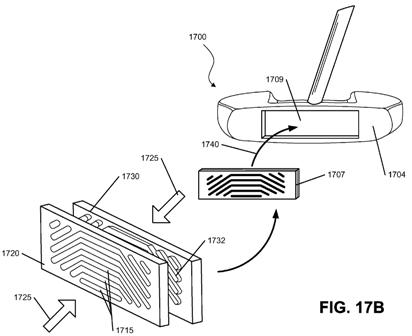
Cool stuff, but I think it is time for the media to put a fork in it; after all, how much free exposure can one product get. Sure makes you appreciate the value of an endorsement from Tiger, even if he eventually switched back to his old putter.
[0084] Other club constructions are possible without departing from this invention, and FIGS. 17A and 17B illustrate another example golf club head 1700 for use with a golf club, such as a putter. Similar to the arrangements described above, the golf club head 1700 includes a front face 1704 including a ball striking surface 1706. In the arrangement of FIGS. 17A and 17B, at least a portion of the ball striking surface 1706 may be formed separately from the remainder of the front face 1704 and may comprise an insert 1707 configured to be received in a recess, such as recess 1709 shown in FIG. 17B, formed in the front face 1704 of the golf club head 1700.
[0085] In at least some examples, the insert 1707 may include a plate, such as a front plate portion 1720, into which grooves of various sizes, configurations, shapes, etc. may be machined or otherwise formed. In some examples, the plate 1720 may be between 1 mm and 4 mm thick and, in some examples, may be approximately 2 mm thick. As mentioned, the plate 1720 may include grooves 1715 formed therein. The grooves 1715 may, in some arrangements, extend completely through the plate 1720 (i.e., forming a through hole in the plate) or may extend partially through the plate 1720. Additionally or alternatively, the grooves 1715 may have a constant depth, width, height, etc. across the plate 1720. However, in some examples, the depth, width, height, etc. of one or more grooves 1715 may vary along the length of the groove 1715, along the plate 1720, and the like. Additionally or alternatively, the grooves 1715, or a portion thereof, may be arranged generally horizontally across the face of the golf club head 1700 when the club is in a ball address position. In other arrangements, the grooves 1715 may extend in a non-horizontal linear, circular, semi-circular, or other curved pattern on the face.
[0086] The plate 1720 may be formed of any suitable material, including metals such as aluminum, steel, titanium, nickel, beryllium, copper, combinations or alloys including these metals, and the like. Once the grooves 1715 are formed in the plate 1720, the plate 1720 may be pressed together ("co-molded") with a moldable, polymer material backing 1730, such as thermoplastic polyurethane or a thermoset material. In some examples, the polymer material 1730 may have a hardness range between 25 and 85 Shore D. In some specific examples, the polymer material backing 1730 may have a hardness range between 35 and 45 Shore D, 50 and 60 Shore D or 60 and 70 Shore D. Forcing the polymer material 1730 together with the front plate 1720 (for example, as indicated by arrows 1725) forms the insert 1707 (as shown in FIG. 17 having polymer material filling the grooves 1715 formed in the plate 1720 to provide a ball striking surface having both metal and polymer contacting the ball. The surface of the polymer backing material 1730 may be pre-formed with projections 1732 to fit into grooves 1715, and/or the polymer material 1730 may be forced into the grooves 1715 during the pressing operation. This combination of metal and polymer materials on the ball striking face may provide improved performance of the golf club including softer feel, increased spin rate, more true roll, a more metallic ball striking sound, etc.
[0087] In some examples, during the pressing or co-molding process, the front surface of the plate 1720 (which will correspond to the face plate of the putter) may be held against a mold surface so that scorelines may be formed in the polymer material. Optionally, if desired, some portion of the scorelines may be cut into the metal portion of the grooves either before or after the co-molding or pressing process. Alternatively, if desired, the score lines may be cut into the polymer and/or metal of the plate after the insert 1707 has been made.
[0088] The insert 1707 may be engaged with a recess 1709 formed in the front face 1704 of the golf club head 1700 (as indicated by arrow 1740) in any desired manner. For instance, the recess 1709 may be milled or otherwise machined into the front face 1704 during manufacture, or it may simply be formed into the desired shape, e.g., during a molding, casting, forging, or other fabrication operation. The insert 1707 may be shaped to correspond to the shape of the recess 1709 and may be configured to be received in the recess 1709. The insert 1707 may be engaged with or connected to the recess 1709 and/or the golf club head 1700 in any desired manner, such as via adhesives and cements; via fusing techniques (e.g., welding, soldering, brazing, etc.); via mechanical fasteners or connectors (including releasable mechanical connectors); and the like. If desired, the insert 1707 may rest on a ledge or other structure defined in the recess 1709 (e.g., along the side, top, and/or bottom edges of the recess 1709).
[0089] In some examples, the insert 1707 may be removable to allow for customization and/or personalization of the insert 1707 and/or golf club head 1700. For instance, the insert 1707 may be releasably connected to the golf club head 1700 using mechanical connectors to secure the insert 1707 in the recess 1709 (e.g., screws, bolts or other connectors may extend from a rear side of the golf club head toward a front region of the golf club head to engage threaded regions provided on the insert 1707, it may be engaged from the bottom surface of the putter upward, it may be engaged from the top surface of the putter downward, etc.). Personalization and customization features may include various characteristics such as polymer and/or metal color (e.g., team colors, color associated with a cause or promotion, player preference, etc.); polymer and/or metal hardness (e.g., harder or softer for different play conditions or swing types); graphics on the polymer and/or metal (e.g., logos, etc.); etc.
[0090] In some arrangements, the metal plate 1720 may be replaced by a plate formed of a polymer of a different hardness from the backing material polymer 1730, thereby forming an insert 1707 of all polymer. For instance, the metal plate 1720 may be replaced with a plate formed of a polymer material having a higher Shore hardness value than the polymer 1730 filling the grooves 1715 of the insert 1707. This all polymer insert may aid in further reducing weight associated with the golf club head 1700. Additionally or alternatively, the polymer material 1730 may be replaced with a metal of a different hardness from the original metal, thereby forming an insert of all metal.
[0091] If desired, the rear surface of recess 1709 may be formed to include a polymer or other material to provide a consistent backing or base against which insert 1707 is mounted. As another alternative, if desired, the material of the polymer backing layer 1730 may be included in the recess 1709 and the club head may be formed by pressing plate 1720 against the polymer backing material 1730 in the recess 1709 to force the polymer material 1730 into the grooves of the plate 1720. If necessary, one or more overflow holes may be provided to allow any excess polymer material 1730 to escape from the club head during the pressing operation.
[0092] In some example, the polymer included in the recess 1709 may be a material different from the polymer material filling the grooves 1715 of the insert 1707. For instance, polymers of different Shore hardness values may be used for the polymer in the recess 1709 and the polymer filling the grooves 1715. In some examples, the polymer filling the grooves 1715 may have a higher Shore hardness than the polymer in the recess 1709. The harder polymer in the grooves 1715 may aid in creating top spin on the ball while the softer polymer in the recess may aid in providing a soft "feel" for the putter.
[0134] FIGS. 26A and 26B illustrate some example effects of various features of this invention, particularly in the presence of the relatively soft polymer fill material in the club head body material (e.g., a thermoplastic polyurethane, which can somewhat grip the ball) and/or a relatively soft ball cover material. More specifically, various advantageous aspects of the invention may be provided by including sharp scorelines in the polymer and/or metal (to provide sharp edges on the putter face that can help grip the ball) and by providing a relatively low loft angle on the putter face (e.g., about 2 degrees as compared to 4 degrees for conventional putters).
[0135] First, as a ball sits on the green, its weight forces it down somewhat into the grass. When putting, the putter must first somewhat "pop" the ball out of this settled condition. Therefore, putter faces generally have some loft to help launch the ball at an upward angle (as mentioned in various arrangements above). This upward angle, however, propels the ball upward (in some instances the ball may actually leave the ground), which causes it to fly or skid across the green before it begins a true roll, as shown in FIG. 26A. This bounce or skid can present some inconsistency in speed, because the ball does not always "fly" or "skid" the same amount, and it can end up taking inconsistent amounts of energy off the ball during the transition between the flying and skidding mode to the rolling mode. In some instances, the loft of the club can actually put a small amount of backspin on the ball.
[0136] Putter structures in accordance with at least some examples of this invention, however, may provide quicker and truer roll as compared to conventional putters. As noted above, because of the soft polymer materials and the sharp edges in the polymer and metal (e.g., from the scorelines), the putter face tends to "grip" the ball a bit better during a putt. This helps "pop" the ball out of its settled condition somewhat more easily and tends to better induce top spin on the ball (which tends to keep the ball on the ground and get it rolling somewhat more quickly). Also, these features allow the putter head to have a less lofted face angle (e.g., 2 degrees vs. a conventional 4 degrees). Thus, the ball does not tend to launch as high out of the settled condition, causing it to more quickly contact the ground once out of the settled position, and the induced top spin gets it rolling more quickly. A schematic diagram of an example trajectory of the ball using an example putter according to this invention is shown in FIG. 26B.
[0137] The microgrooves, as described in conjunction with the arrangement illustrated in FIGS. 25A-25C can also enhance the ball grip and imparting top spin on the ball.
[0138] As shown in FIGS. 26A and 26B, putters in accordance with examples of this invention may get the ball rolling much earlier during the course of a putt (e.g., within about 2 inches or less for the putters according to the invention vs. at about 4 to 5 inches for conventional putters). Moreover, by getting the ball rolling earlier, with less bounce and skid (and the uncertainty introduced into the putt due to these undesired factors), putters in accordance with examples of this invention tend to provide more reliable and repeatable putting distances, putted ball speeds, and distance control.
[0139]Moreover, the combination of metal and polymer on the face of the putter provides a nice, soft and consistent feel (optionally controllable by selecting the hardnesses of the various parts) while still providing a more conventional "metal-on-ball" sound (or "click") of conventional putters. This sound feature also is an important part of the "feel" for many golfers, and maintaining this metallic sound helps prevent a more "dead" sound of putting a ball against a full polymer material on a putter face (e.g., as provided in many conventional putters that simply have a polymer insert).
Dave Dawsey - Watching Golf Putting Patents
PS – check out additional putter patents HERE
Comments